How Laminate Is Made
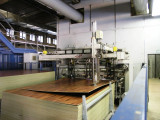
Construction of a Laminate Floor Board
Laminate flooring is made out of a few different layers, usually four, of different materials, each giving the final board some of its features. The look of your laminate comes from photographic layer, for instance. These are combined into a single plank and “thermofused”, literally fused together with high heat and pressure. This is done in either a one step or a two step process. The one step process is called Direct Pressure Laminate (DPL), in which all of the layers are joined together at one time. The two step process is called High Pressure Laminate. With this process, a couple of layers are prepared first to boost some of their qualities, and then the sets of layers are assembled into the final piece.
The four basic laminate flooring construction layers
Core Board or “Inner Core Layer”
This is the thickest layer. If you were able to make a plank of laminate by hand, you would probably think of this as the actual board to which you would be sticking the other, thinner layers. This central layer gives the floor its strength, sturdiness, stability and impact resistance. It is usually made of High Density Fiberboard (HDF), an engineered product which includes wood, but has extra durability. HDF is composed of leftover material from wood processing factories, sawdust, wood chips, things like that. This is part of the reason we consider laminate flooring an environmentally friendly product – trees are not cut down to provide these materials
This material is ground up, and a melamine resin is added. Melamine is a synthetic resin made from an organic compound. It is used to increase durability, and add moisture resistance. All of this material is dried and formed into HDF panels. Sometimes a water resistant sealer is used on the board to further protect the final product from moisture. If not HDF, the core might be made of a medium density fiberboard, high density wood particle core (this absorbs glue better than HDF, and might be used for some glue together products) or even plastic.
The core is the basic structure of the laminate product. It’s the base for the top layers, the image and finish, and it is the part of the plank onto which the tongues and grooves that make the locking system are formed.
Backing or “Stabilizing Layer”
Completing the real structure of the plank is the bottom layer. It can be made of paper, but usually is made of a melamine plastic. This bottom layer helps protect the rest of the board from rising moisture, and adds strength and stability to keep a plank from warping. It may also have a water resistant sealer applied before being combined with the other layers.
These first two layers make up the base of the board and give you the thickness of your laminate flooring. Generally, thicknesses of the board itself will range from 6mm to
12mm. Thicker planks are stronger, of course, but also more rigid. This helps your finished floor overcome any minor subfloor irregularities.
The surface is also made of two layers, the photograph and the finish.
Photographic Image Layer, Decorative Layer or Print Film
The image is the next layer up from the core board, applied directly to it. It is a very high resolution picture printed onto a melamine impregnated paper. Usually the image will feature a real hardwood plank, but ceramic tile, natural stone and other materials can also be replicated with this photographic layer. If the top layer is texturized, not only the look, but the feel of the board can be quite authentic.
Wear Layer or “Overlay”
This is the “finish” of a board of laminate, the clear, top coating which provides not only the gloss level, but also protection for the image below it. It is usually made of several coats of melamine, aluminum oxide, or a combination of the two. You will see references to aluminum oxide being the second hardest substance known to man, after the diamond. That is not exactly correct, but the fact that it is a subject of debate means that aluminum oxide is still pretty tough stuff. After the layer combining heat and pressure are applied, this top layer becomes very durable, resisting abrasion, scratching, scuffing, staining, burning, wear and even the fading of the image below.
![]() Forming the PiecesOnce the decorative elements are complete, the sheets of laminated material are cut into either square tiles or planks. The tongues and grooves which make up the locking system are cut into all four edges of the boards using special equipment. If the installation system will require glue, a special adhesive activated on site by application of water may be applied to the grooves. Finally any padding which may be included will be attached to the backing layer. |
– – – –
David has written and made videos about flooring products and installation since 2011 at Floors To Your Home (.com), where he is also the PPC Manager, a Researcher, a Website & Marketing Strategy Team member, Videographer, Social Strategist, Photographer and all around Resource Jito. In my spare time I shoot and edit video, put together a podcast, explore film history, and mix music (as in ‘play with Beatles multi-tracks’). Connect with
W. David Lichty
Follow Team Floors To Your Home on Facebook